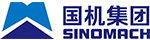
文章出處:知識(shí)中心 網(wǎng)責(zé)任編輯: 洛陽軸承 閱讀量: 發(fā)表時(shí)間:2021-05-21 17:11:48
要滿足軸承性能要求,以淬火硬化為目的的熱處理是不可少的工序。熱處理工序中所消耗的能源占軸承制造工序總能耗的25%左右。因此,從節(jié)能、環(huán)保角度,對(duì)軸承制造過程中的熱處理進(jìn)行分析,主要的對(duì)策包括:熱處理工序的高效化;小變形熱處理技術(shù)等。
1 軸承的熱處理方法
以淬火硬化為目的的軸承熱處理方法有多種,多數(shù)情形下可大致分為整體淬火、滲碳淬火、高頻淬火、碳氮共滲等。
整體淬火是最普通的軸承熱處理工藝,材料多數(shù)使用高碳鉻軸承鋼(GCr15)。在熱處理爐中加熱到840 ℃左右,并使球化退火所形成的碳化物在基體中適度、均勻地固溶,進(jìn)而淬火冷卻后,實(shí)施低溫回火。通過未溶碳化物與回火析出的碳化物,獲得均勻的析出組織,可用于要求耐磨的軸承。
滲碳淬火是在熱處理爐中將低碳合金鋼于930 ℃左右保溫,管理爐內(nèi)的滲碳性氣體,從表面到內(nèi)部使碳滲入擴(kuò)散,進(jìn)行淬火的熱處理,由于碳濃度的梯度,淬火后的表面硬化,因內(nèi)部比表面硬度低,用于要求耐沖擊性的軸承。
高頻淬火是利用感應(yīng)加熱的熱處理,主要用于中碳鋼,應(yīng)用于形狀復(fù)雜的汽車車輪用軸承等,只硬化必要部位。
碳氮共滲是在滲碳性氣體中添加5%左右的氨,在表面層附近析出氮化物??紤]到,奧氏體中的碳與氮的溶解度差異,通常是在低于滲碳溫度的750~850 ℃下進(jìn)行處理,尤其是對(duì)于在混入異物的環(huán)境下使用的軸承的長(zhǎng)壽命化最有效。
2 熱處理高效化(壓縮滲碳時(shí)間)
在滲碳淬火熱處理中,尤其要求通過高效化以實(shí)現(xiàn)節(jié)能,與整體淬火的處理時(shí)間相比,滲碳淬火的處理時(shí)間長(zhǎng)達(dá)前者的幾倍到數(shù)十倍(處理時(shí)間隨著軸承尺寸不同而有差異,但大尺寸軸承有時(shí)候要在爐中經(jīng)過將近100 h的處理),因此消耗較多的能源,為降低能耗,縮短滲碳時(shí)間是有待解決的一大課題。
氣體滲碳廣泛應(yīng)用于批量生產(chǎn)。通常,按照滲碳的機(jī)理,一般認(rèn)為有2個(gè)階段。在第1階段是由于滲碳?xì)怏w與鋼材的滲碳反應(yīng),碳向鋼材表面移動(dòng)的階段;第2階段,滲碳?xì)怏w與鋼材表面的碳勢(shì)大致相等之后,鋼材表面的碳向內(nèi)部擴(kuò)散,表面碳勢(shì)降低,由滲碳?xì)怏w補(bǔ)充,要縮短滲碳時(shí)間有必要提高第1,2階段的速度。
使用普通的RX氣體進(jìn)行氣體滲碳時(shí),為加速其第1階段的滲碳,一般要加大滲碳?xì)怏w中的CO, H2的分壓力。近年來,正在著眼于改變滲碳?xì)怏w中所含CO, H2的分壓力,開發(fā)旨在提高滲碳速度、壓縮滲碳時(shí)間的技術(shù)此外,作為替代氣體滲碳的滲碳工藝,通過在稱為真空滲碳的低壓氣氛中,使少量的碳化氫系氣體直接與工件接觸,以進(jìn)行滲碳,提高碳在鋼表面的滲入速度。
在碳擴(kuò)散的第2階段,由于碳的擴(kuò)散依賴于溫度,通過提高滲碳溫度,可以大幅度縮短滲碳時(shí)間。不過,由于滲碳溫度高,晶粒粗大化等重要原因,會(huì)導(dǎo)致機(jī)械性能降低,所以,滲碳溫度存在不能超過晶粒粗化極限溫度的問題。開發(fā)可解決上述問題的材料也是解決問題的途徑。
從材料方面考慮,需開發(fā)新的材料,即容易使碳滲入鋼材表面的材料。此外,通過使用高淬透性的材料,使有效硬化層深度加深,能縮短滲碳時(shí)間,但目前來看,這樣的新材料價(jià)格較高。
3 小變形熱處理技術(shù)
熱處理過程中會(huì)發(fā)生變形,熱處理后的變形量決定了后續(xù)磨削工序(圖1)的磨削余量。軸承的制造工序中,僅次于熱處理能耗的是磨削、組裝工序,通過減小磨削余量可壓縮磨削的循環(huán)時(shí)間,降低熱處理變形關(guān)系到削減大量能耗。
圖1 軸承的普通制造工序
以軸承鋼熱處理時(shí)的尺寸變化(圖2)為例,隨著加熱時(shí)的溫升,發(fā)生熱膨脹與奧氏體化,并在冷卻時(shí)產(chǎn)生熱收縮,馬氏體相變時(shí)產(chǎn)生熱處理變形。這樣一來,熱處理時(shí)有很多引起尺寸變化的要素,由于該尺寸變化時(shí)產(chǎn)生偏差,而發(fā)生熱處理變形。該尺寸變化的偏差,是加熱、冷卻時(shí)的溫度偏差引起,均勻地加熱、冷卻可降低熱處理變形。
為此,防止熱處理變形的對(duì)策有以下幾種:以降低加熱時(shí)的溫度不均為目的的多級(jí)升溫;以降低冷卻時(shí)的溫度不均為目的的多級(jí)冷卻;還有淬火油種類、油槽攪拌速度的最優(yōu)化之類的措施。近年來,也在采取其他對(duì)策:如,通過模擬熱處理時(shí)油槽內(nèi)的油液流動(dòng),進(jìn)行分析,開發(fā)形成均勻油液流動(dòng)的油槽;通過改善熱處理夾具,能實(shí)現(xiàn)均勻加熱、冷卻。
此外,尤其在容易發(fā)生熱處理變形的薄壁軸承方面,根據(jù)熱處理時(shí)溫度與尺寸變化的關(guān)系(圖2)進(jìn)行淬火(壓模淬火)。如果是軸承鋼,經(jīng)整體淬火引起的相變導(dǎo)致尺寸膨脹,在Ms點(diǎn)之后,約束外徑側(cè),并用壓力機(jī)一邊控制工件上下方向,一邊完成淬火。由于滲碳淬火完成后尺寸幾乎沒有改變,淬火過程中發(fā)生熱收縮,一邊用壓力機(jī)控制并約束內(nèi)徑側(cè),一邊實(shí)施淬火,進(jìn)而大幅度地降低熱處理變形(圖3)。
在熱處理的尺寸變化時(shí),利用該變化進(jìn)行約束淬火是降低熱處理變形的有效對(duì)策之一。軸承并不像齒輪那樣形狀復(fù)雜,由于形狀簡(jiǎn)單,一直在實(shí)施約束淬火,不過,約束淬火的熱處理成本比普通熱處理費(fèi)用高是有待解決的問題。
圖2 熱處理時(shí)溫度與尺寸變化
圖3 約束淬火方法
因此,開發(fā)出不產(chǎn)生熱處理變形的熱處理技術(shù),是一項(xiàng)有意義的研究工作。針對(duì)影響鋼材變形的因素,也可采取適當(dāng)?shù)膶?duì)策,例如,減少材料偏析,在不進(jìn)行鍛造工序時(shí),降低材料的殘余應(yīng)力等。
小結(jié)
上面闡述了軸承的幾種典型熱處理方法,與以節(jié)能為目的的高效化與低變形熱處理技術(shù),但為了適應(yīng)減輕環(huán)境負(fù)擔(dān)的要求,熱處理工序方面發(fā)揮更大的作用,進(jìn)一步提高技術(shù)水平是不可缺少的,有必要以節(jié)能為核心,進(jìn)一步實(shí)現(xiàn)低成本化。
(來源:軸承雜志社)
軸研所公眾號(hào) 軸承雜志社公眾號(hào)
營(yíng)銷熱線
0379-64367521
0379-64880626
13693806700
0379-64880057
0379-64881181