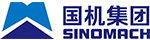
文章出處:知識(shí)中心 網(wǎng)責(zé)任編輯: 洛陽軸承 閱讀量: 發(fā)表時(shí)間:2021-06-16 08:37:19
導(dǎo)讀
剖分三排圓柱滾子轉(zhuǎn)盤軸承分段多,尺寸大,質(zhì)量大,加工時(shí)裝配精度低,整圈淬火變形大,接縫處應(yīng)力大,徑向及圓周方向間隙不易調(diào)整,配制游隙時(shí)修磨滾道次數(shù)多,傳統(tǒng)高速鋼材料刀刃易磨損。提出改進(jìn)措施:加工和拼接時(shí)增加專用胎具;采用分段、分面淬火,淬火后增加整形工序;設(shè)計(jì)徑向定位夾具調(diào)整徑向間隙,設(shè)計(jì)切向定位夾具調(diào)整圓周方向間隙;通過軸向游隙推算所需加工的內(nèi)、外圈軸向滾道尺寸;軟車采用帶涂層的硬質(zhì)合金刀具,硬車采用立方氮化硼(CBN)刀具完成以車代磨等。最終確定的工藝路線滿足了軸承加工所需的技術(shù)要求。
隨著海工裝備技術(shù)日趨成熟,海工行業(yè)大型起重機(jī)已經(jīng)向超大尺寸、超大噸位發(fā)展,與其配套的轉(zhuǎn)盤軸承直徑達(dá)10 m以上。該直徑段的轉(zhuǎn)盤軸承結(jié)構(gòu)多為剖分式,其優(yōu)點(diǎn)是便于運(yùn)輸、儲(chǔ)存及拆裝,缺點(diǎn)為需要多次拆分、拼接,加工工藝復(fù)雜,加工精度難以保證,故需確定合適的加工工藝。
1、超大型剖分三排圓柱滾子轉(zhuǎn)盤軸承結(jié)構(gòu)
某剖分三排圓柱滾子轉(zhuǎn)盤軸承結(jié)構(gòu)如圖1所示,采用階梯搭接,軸向用鉸制螺栓定位連接(圖2)的方式組合成整體內(nèi)、外圈,裝配后軸承內(nèi)圈沿內(nèi)徑方向展開如圖3所示。
該剖分軸承最大外徑為12.3776 m。高度為0.6 m,最大壁厚為489 mm,內(nèi)外圈共分為18段。技術(shù)要求:裝配高為(600士2) mm,軸向游隙為1.2 ~1.8 mm,徑向游隙為0.5 ~1.2 mm,軸向跳動(dòng)不大于0.6 mm,徑向跳動(dòng)不大于2 mm。
1)軸承直徑超出機(jī)床工作臺(tái)加工范圍。
2)在推力滾道上剖分切口會(huì)與滾子素線形成一定夾角,使?jié)L子能通過切口。為保證齒輪強(qiáng)度受影響小,將外齒圈剖分切口切在齒槽底中心位置,增大了銑連接面及拼接整圓的難度。
3)剖分軸承直徑大,加工過程中剖分段因自重下墜傾斜,兩端面及軸向滾道平面度、傾斜度大,徑向滾道圓度、圓柱度超出工藝要求,裝配后軸承旋轉(zhuǎn)精度不能滿足要求。
4)外齒圈淬火面總長(zhǎng)度為490 mm,屬大截面滾道淬火。整圈淬火時(shí)剖分段會(huì)出現(xiàn)不規(guī)則變形(圖4),變形后無法拼接成整圓,影響后序加工。整圈淬火后接縫處應(yīng)力較大,套圈會(huì)從接縫處脫開。整圈尺寸大,淬火機(jī)床回轉(zhuǎn)困難。
3、方案制定
3.1 工裝夾具
剖分軸承在胎具上加工,為便于吊裝,胎具也采用剖分結(jié)構(gòu)。整個(gè)胎具分為4段,連接方式為上下搭接,軸向用錐銷定位,加雙排螺釘緊固(圖5)。
胎具材料選用具有較高屈服強(qiáng)度和抗拉強(qiáng)度的ZG380-510鑄鋼,保證胎具剛度胎具為剖分軸承加工提供了可靠的剛性支承,可減小各工序加工變形,保證加工精度。
為拓展機(jī)床加工范圍,重新制作專用方箱、支座以及配套的T形塊、螺桿、擋板、壓板、墊塊等,解決了大直徑軸承超范圍加工問題。
3.2 裝夾方式
加工時(shí)要考慮胎具與剖分軸承的裝夾方式,以內(nèi)圈主推力滾道加工為例,內(nèi)圈裝夾如圖6所示。方箱底部設(shè)計(jì)2排連接孔,通過螺栓與機(jī)床工作臺(tái)連接??ㄗ⑻ゾ呖ňo并用壓板固定。內(nèi)圈放置在胎具上,長(zhǎng)擋板頂緊外徑面,壓板壓緊內(nèi)圈端面。胎具和內(nèi)圈進(jìn)行軸向和徑向定位,固定點(diǎn)數(shù)量是軸承分段數(shù)的3倍,防止零件加工中出現(xiàn)平移。
3.3 拼接整圓
剖分面為臺(tái)階形狀,要求拼接軸向間隙不大于0.1 mm,徑向間隙不大于0.3 mm。拼接會(huì)影響軸承加工精度,因此要保證外齒圈剖分切口在齒槽底中心位置。工藝上選擇先劃出成品齒形及精銑連接面剖分線(圖7),其軸向和圓周貼合面均在數(shù)控龍門銑床上加工。通過程序設(shè)定、預(yù)先模擬調(diào)整每段弧長(zhǎng)及2個(gè)結(jié)合面的角度和尺寸,多次研配結(jié)合面以確保連接精度,待連接整圓后依次配對(duì)編號(hào)。
剖分軸承在加工中需多次吊裝、拼接、拆分,為保證成品連接精度,在前工序加工時(shí)采用小尺寸的工藝錐錐孔。通過錐銷對(duì)每段連接點(diǎn)定位后連接加工。終加工時(shí)將定位錐銷孔加工成鉸制螺栓孔,保證零件連接可靠。
3.4 淬火方案
選取分段、分面淬火。為方便吊裝,淬火前加工吊裝孔。為減小淬火變形,在套圈上設(shè)置端面臺(tái)階,胎具設(shè)置凹槽(配合間隙1~2 mm)進(jìn)行限位。另外,在胎具上加工與套圈吊裝孔位置一致的螺紋孔,用螺釘將套圈與胎具固定(圖8)。
3.5 整形方案
淬火后每段曲率不規(guī)則,不成正圓,總趨勢(shì)為外圈弦長(zhǎng)減小,內(nèi)圈弦長(zhǎng)增大。套圈壁厚較大,淬火后需進(jìn)行熱整形。整形要求如下:
1)對(duì)比淬火前、后每段弦長(zhǎng)變化,確定整形量,選定整形位置;
2)火焰溫度為700~800℃,加熱時(shí)控制加熱面積,防止產(chǎn)生新的變形,加熱后澆注冷卻液;
3)粗整形,以實(shí)際弦長(zhǎng)為依據(jù)(不需要在機(jī)床上進(jìn)行);
4)精整形,邊整形邊測(cè)量每段圓周跳動(dòng)(在機(jī)床上進(jìn)行) ,使每段均符合工藝要求;
5)整形后測(cè)量每段尺寸是否達(dá)到整形要求。
3.6 裝配方案
剖分軸承精加工、裝配均以淬火、 整形后每段連接面處軸向、徑向間隙做為拼接基準(zhǔn)。裝配方案:先吊取第2內(nèi)圈,按編號(hào)依次完成拼接,通過徑向定位夾具調(diào)整徑向間隙(圖9),通過周向定位夾具(圖10)調(diào)整圓周方向間隙,然后用校對(duì)樣板內(nèi)圈半徑R2(圖11)校驗(yàn)接縫處曲率,通過鉸制螺栓連接,完成第2內(nèi)圈裝配。再按照常規(guī)三排圓柱滾子轉(zhuǎn)盤軸承的裝配方法組裝成整套軸承。內(nèi)、外圈裝配方法參考第2內(nèi)圈。
調(diào)整徑向間隙時(shí),將夾具放置在套圈端面上,螺桿頂緊軸承內(nèi)、外徑面,通過螺桿調(diào)節(jié)。調(diào)整圓周方向間隙時(shí),將螺紋孔定位銷與光孔定位銷分別放在連接縫處的2個(gè)安裝孔內(nèi),通過螺桿緊固調(diào)節(jié)。
3.7 軸承游隙
通過軸向游隙推算所需加工的內(nèi)、外圈軸向滾道尺寸,可減少滾道修磨次數(shù),從而減少吊裝、拼接次數(shù),提高加工效率。軸向游隙計(jì)算示意圖如圖12所示,軸向游隙Ga=b+c-a-d-d2。
剖分軸承分段拼接,每段外齒圈會(huì)因自重下墜傾斜,普通三點(diǎn)測(cè)量軸向游隙已不適用。軸向游隙測(cè)量如圖13所示,虛線、實(shí)線分別為軸承組裝后的實(shí)際位置和理論位置。千斤頂與百分表位置均會(huì)對(duì)軸向游隙產(chǎn)生影響,測(cè)得A點(diǎn)值比B點(diǎn)大,B點(diǎn)值更接近實(shí)際游隙。采用單點(diǎn)測(cè)量軸向游隙,千斤頂與百分表位置靠近軸承內(nèi)圈,在每段中間部位及連接縫處各取1個(gè)點(diǎn),共計(jì)12個(gè)點(diǎn)或更多,取其平均值作為實(shí)測(cè)軸向游隙。
徑向游隙的配制:試配初始徑向游隙→確定滾子尺寸→修磨滾子。
徑向游隙的測(cè)量:第2內(nèi)圈、軸向滾子與外圈裝配后,在連接縫處及每段中間部位(共計(jì)12處),裝入徑向滾子(為保證徑向游隙測(cè)量準(zhǔn)確,采取無間隔并排滾子,要求每組滾子數(shù)量不少于30粒),測(cè)量徑向滾子與內(nèi)、外圈間隙,取其平均值作為實(shí)測(cè)徑向游隙。
3.8 選擇刀具及加工參數(shù)
精加工余量小,可使用帶涂層的硬質(zhì)合金刀具完成車削,該刀具硬度達(dá)69~81 HRC,車削平穩(wěn),耐磨性好,切削速度是普通高速鋼的4~7倍,提高了加工效率。硬質(zhì)合金刀具加工參數(shù)為:機(jī)床轉(zhuǎn)速2 r/min, 進(jìn)給量0.4~0.7 mm/r。
滾道表面淬火后硬度為57~62 HRC,終磨滾道前先硬車去除滾道淬火變形較大部位,可減小后續(xù)磨加工留量,大幅提高加工效率。硬車使用立方氮化硼(CBN)刀具完成以車代磨。CBN是超硬刀具材料,硬度高和耐磨性好,用于對(duì)淬硬鋼(硬度45~65 HRC)的精加工,也可用于精車斷續(xù)表面,但在斷續(xù)加工中,不能使用冷卻液。CBN刀具加工參數(shù)為:機(jī)床轉(zhuǎn)速2.5 r/min, 進(jìn)給量0.08~0.2 mm/r。
4、確定工藝流程
4.1 初步工藝流程
根據(jù)剖分軸承的結(jié)構(gòu)特點(diǎn),初步確定工藝流程:鍛件→粗車→銑連接面→拼接整圓→鉆、鉸工藝錐銷孔→半精車→滾道表面淬、回火→整形→精車→鉆孔→硬車滾道→終磨→配游隙→裝配。
該流程存在以下問題:
1)粗車切除材料較多,應(yīng)力不能完全釋放;
2)淬火后變形量(端面翹曲、徑向跳動(dòng))大,影響后序加工;
3)熱整形溫度高,整形部位有較大內(nèi)應(yīng)力,易出現(xiàn)裂紋。
4.2 優(yōu)化工藝流程
對(duì)上述問題分析,認(rèn)為剖分軸承加工重點(diǎn)是要控制熱處理變形,保證整形質(zhì)量,最終確定優(yōu)化后的工藝流程為:鍛件→粗車→去應(yīng)力退火→半粗車→粗銑連接面→振動(dòng)時(shí)效→精銑連接面→拼接整圓→鉆、鉸工藝錐銷孔→半精車→鉆、攻吊裝孔→附加回火(溫度170 ℃±10 ℃,爐內(nèi)保溫4 h±0.5 h)→滾道表面淬、回火(溫度170 ℃±10 ℃,爐內(nèi)保溫8 h±0.5 h)→整形→附加回火→精車→鉆孔→硬車滾道→終磨→配游隙→裝配。
優(yōu)化后的工藝流程具有以下優(yōu)點(diǎn):
1 )淬火前增加附加回火,可及時(shí)消除或減小前工序產(chǎn)生的殘余應(yīng)力,進(jìn)而減小淬火變形;
2)熱整形后增加附加回火,可防止整形開裂。
5、實(shí)際加工效果
采用優(yōu)化工藝加工后軸承的各項(xiàng)技術(shù)指標(biāo)檢測(cè)結(jié)果見表1,滿足技術(shù)要求。軸承交付使用后,未發(fā)現(xiàn)異?,F(xiàn)象。
(來源:《軸承》2021年6期)
軸研所公眾號(hào) 軸承雜志社公眾號(hào)
營(yíng)銷熱線
0379-64367521
0379-64880626
13693806700
0379-64880057
0379-64881181